Different types of timber cuts
In the world of woodworking, crafting timber transcends carpentry but the final plank aesthetic first begins with how you cut the timber trunks.
Various sawing techniques result in different grain patterns and contributes to the overall grade of the timber.
Cedar Log
200-year old roundel
The initial sawing is key as it has enormous bearing on what the log should become and is essentially the first unveiling of the wood. The thickness, direction of the cut and positioning of the log need to be handled sensitively but with intent. Has the tree grown vertically or has it twisted as it grew, are there knots and burls that will add character and depth?
There are a number of ways that the logs can be sawn, including plain, live, quarter or rift.
PLAIN SAWN
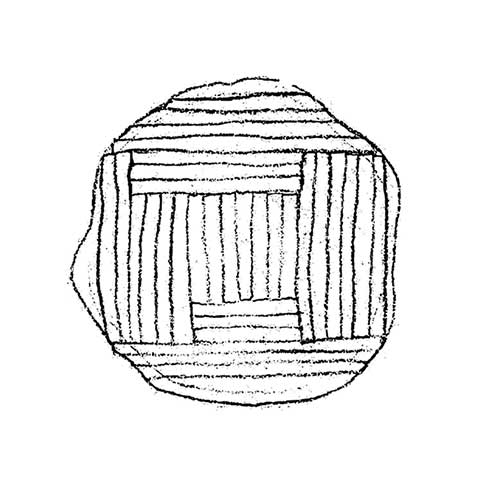
Most common sawing method. Fast to produce with little waste.
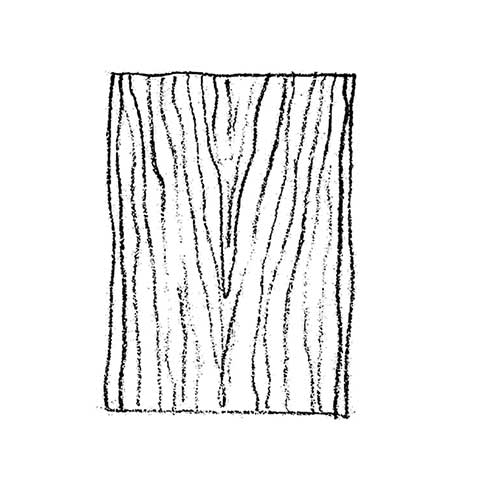
Narrow range of grain patterns.
A Plain Sawn floor example
Ryhill Extra Wide Plank
A board with growth rings running roughly parallel – usually in arches – relative to the face of the board is called a plain-sawn (or flat-sawn) board.
LIVE SAWN
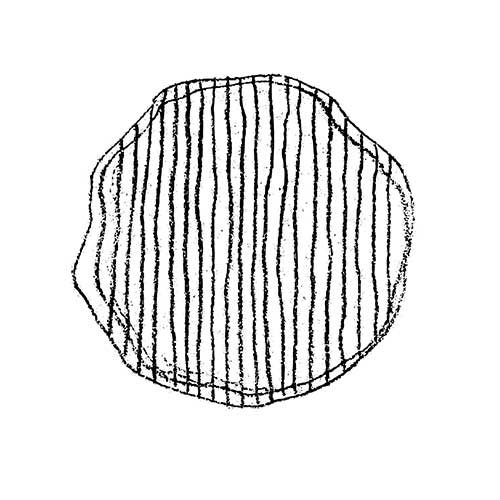
Traditional sawing method with a blended mix of all cuts.
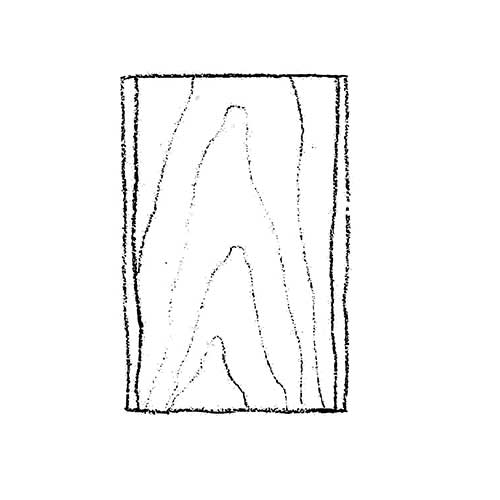
Broad range of grain patterns, including quarter & rift sawn.
A Live Sawn floor example
Elias Random Width Planks
Live sawn timber cuts produce planks that showcase the full spectrum of grain patterns and natural characteristics from the entire cross-section of a tree, providing a unique and visually appealing appearance.
QUARTER SAWN
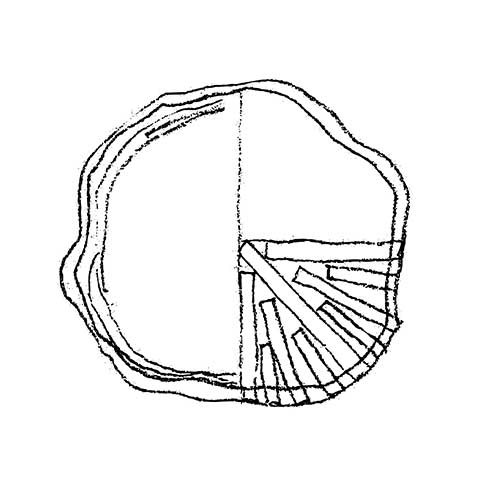
High end sawing method which produces narrower boards, grain 90 degrees to the surface.
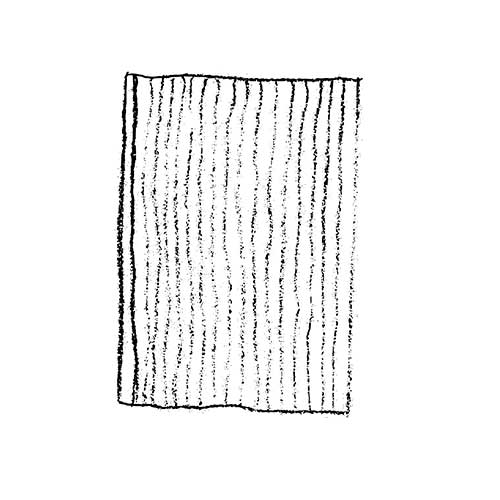
Mainly straight grain with silvery medullary rays.
A Quarter Sawn floor example
Galion Random Width Plank
If the growth rings are at a steep angle relative to the face, the board is said to have quarter sawn grain.
RIFT SAWN
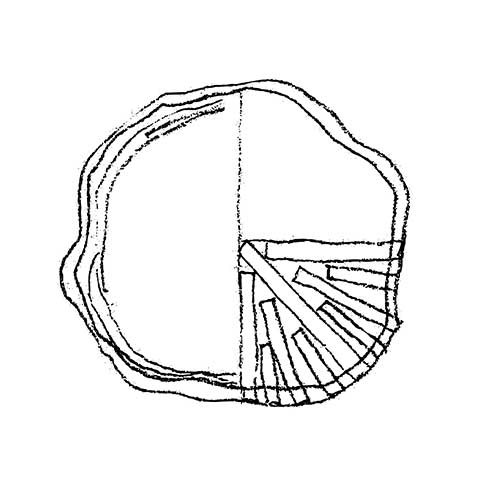
Rare sawing method in which the boards milled perpendicular to the growth rings.
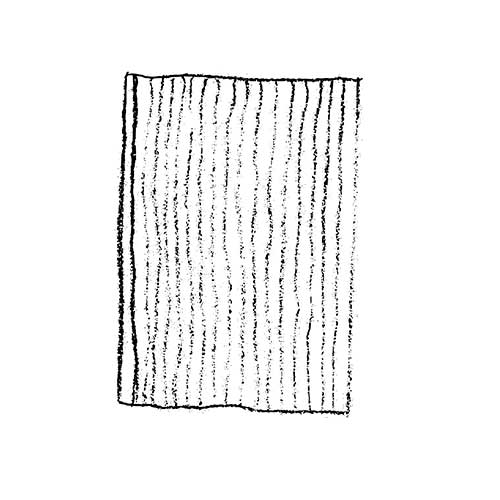
Very tightly grained
A Rift Sawn floor example
Merrain Random Width Plank
If the growth rings run at a slightly lower angle, it’s called rift-sawn. It is produced by milling perpendicular to the log’s growth rings producing a linear grain pattern but also results in the most waste, increasing the cost and is therefore a less common approach.